Cable production
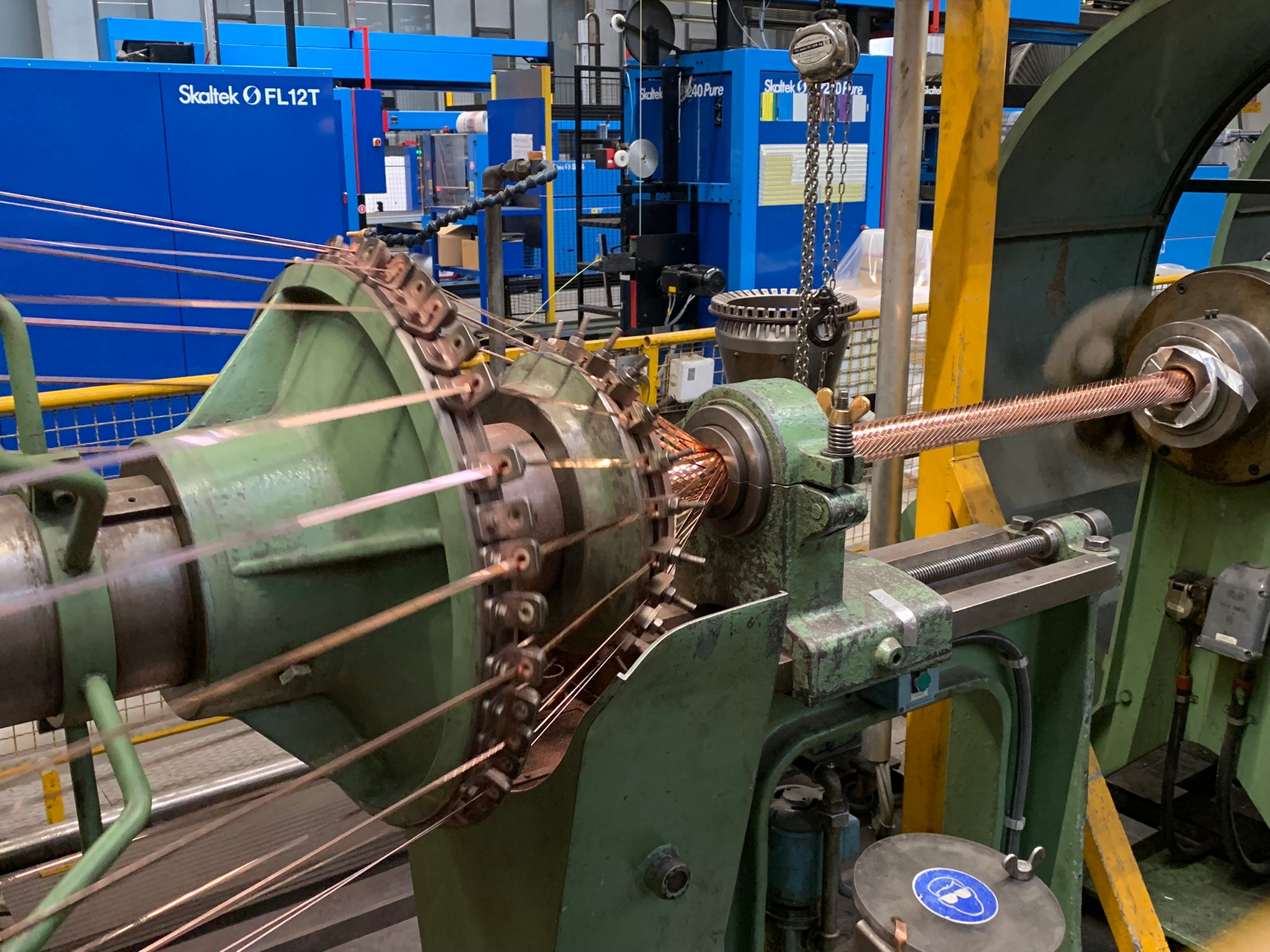
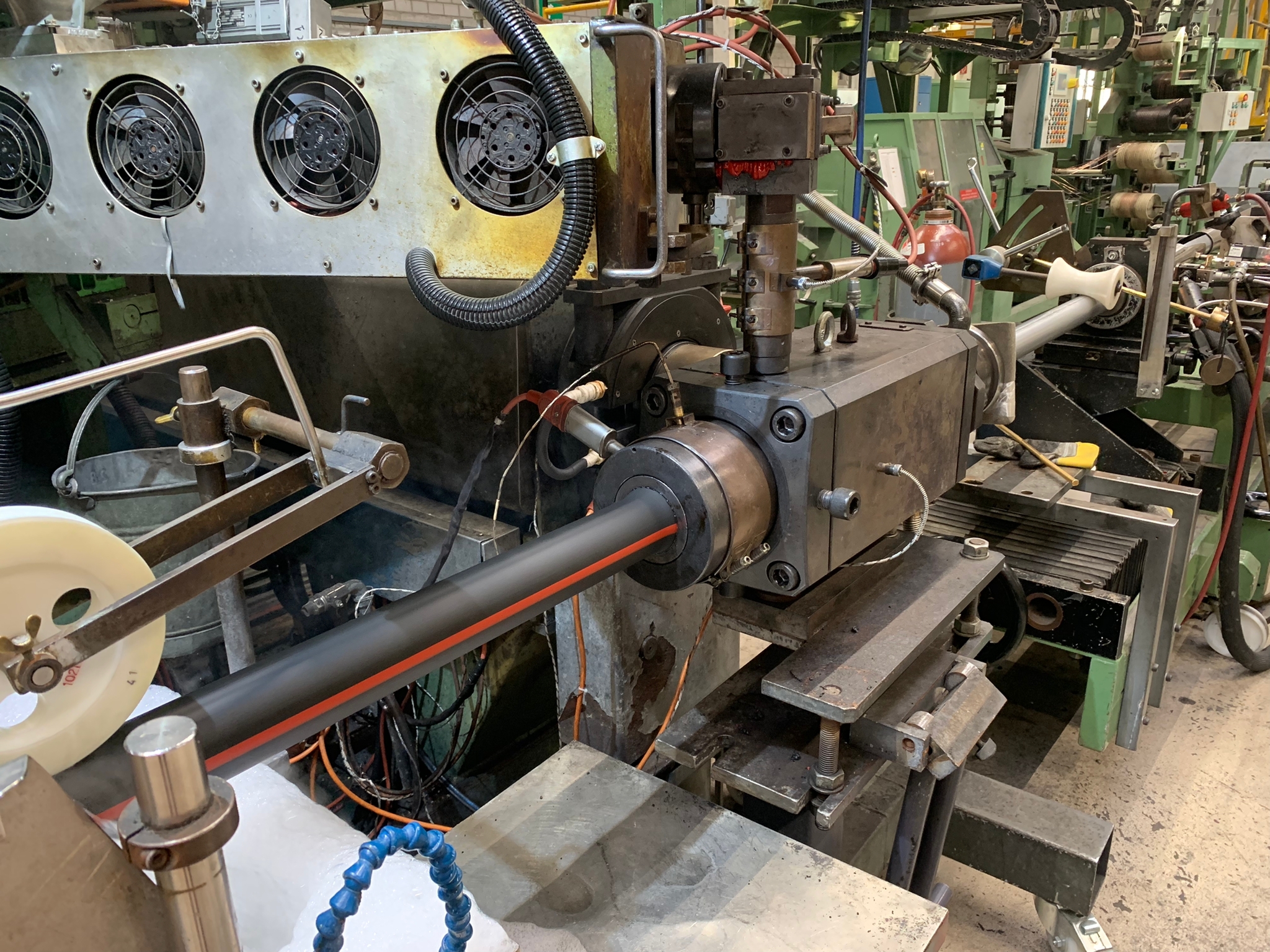
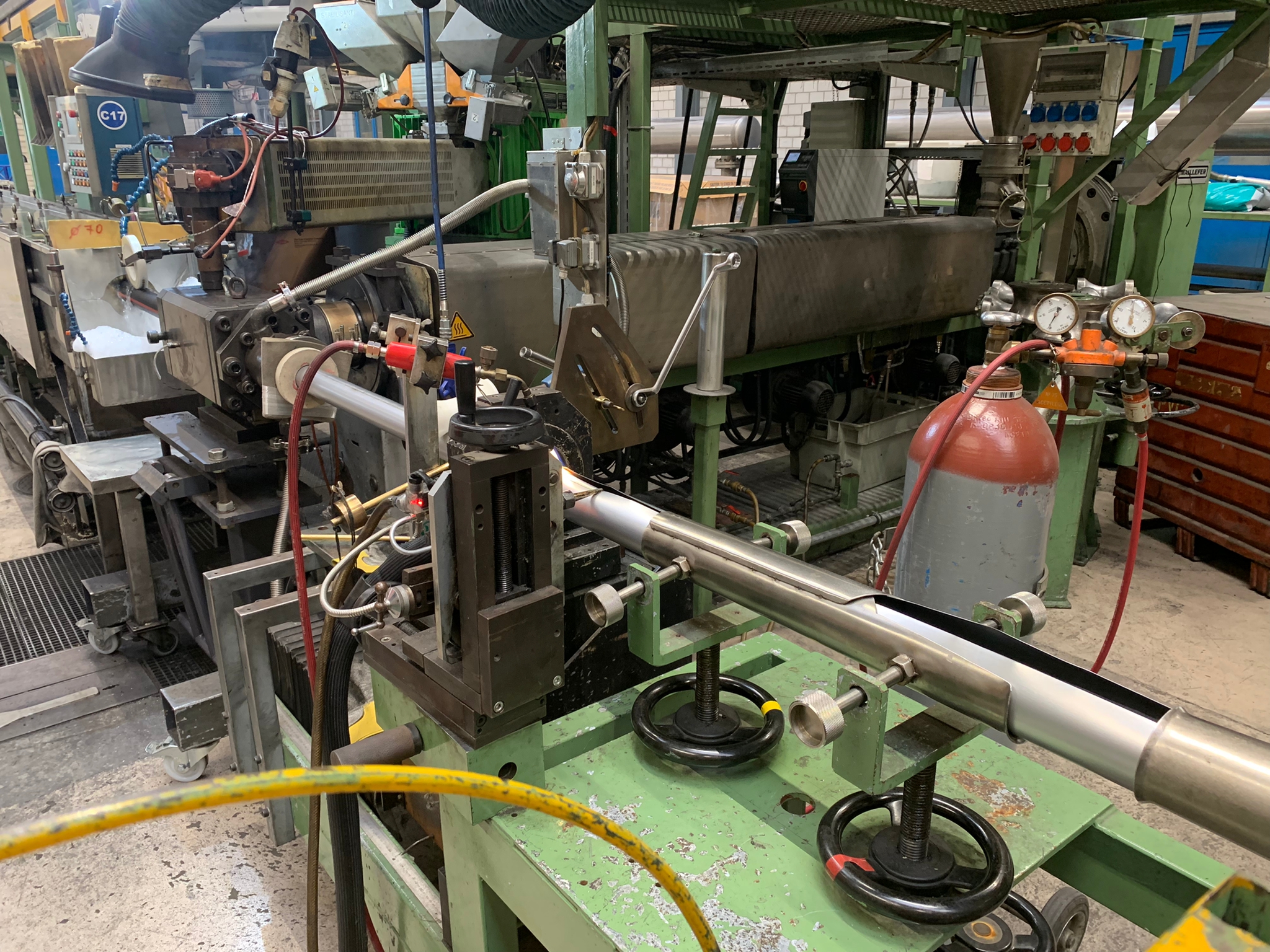
copper drawing
The copper mill produces 8mm thick and about 3-5t heavy copper coils. First the coils are drawn in three stages, raw drawing, medium and fine drawing through numerous drawing dies.In doing the external diameter of decreases only by a minimum each time until the wire is stretched to a diameter of e.g. 0.05 mm.
Stranding
All conductors are combined into one strand and optionally covered by a foil.This foil protects the insulation from Damage,if the cable is fitted with an electromagnetic shielding.
Shielding
Sheathing
Final Inspection
Packaging
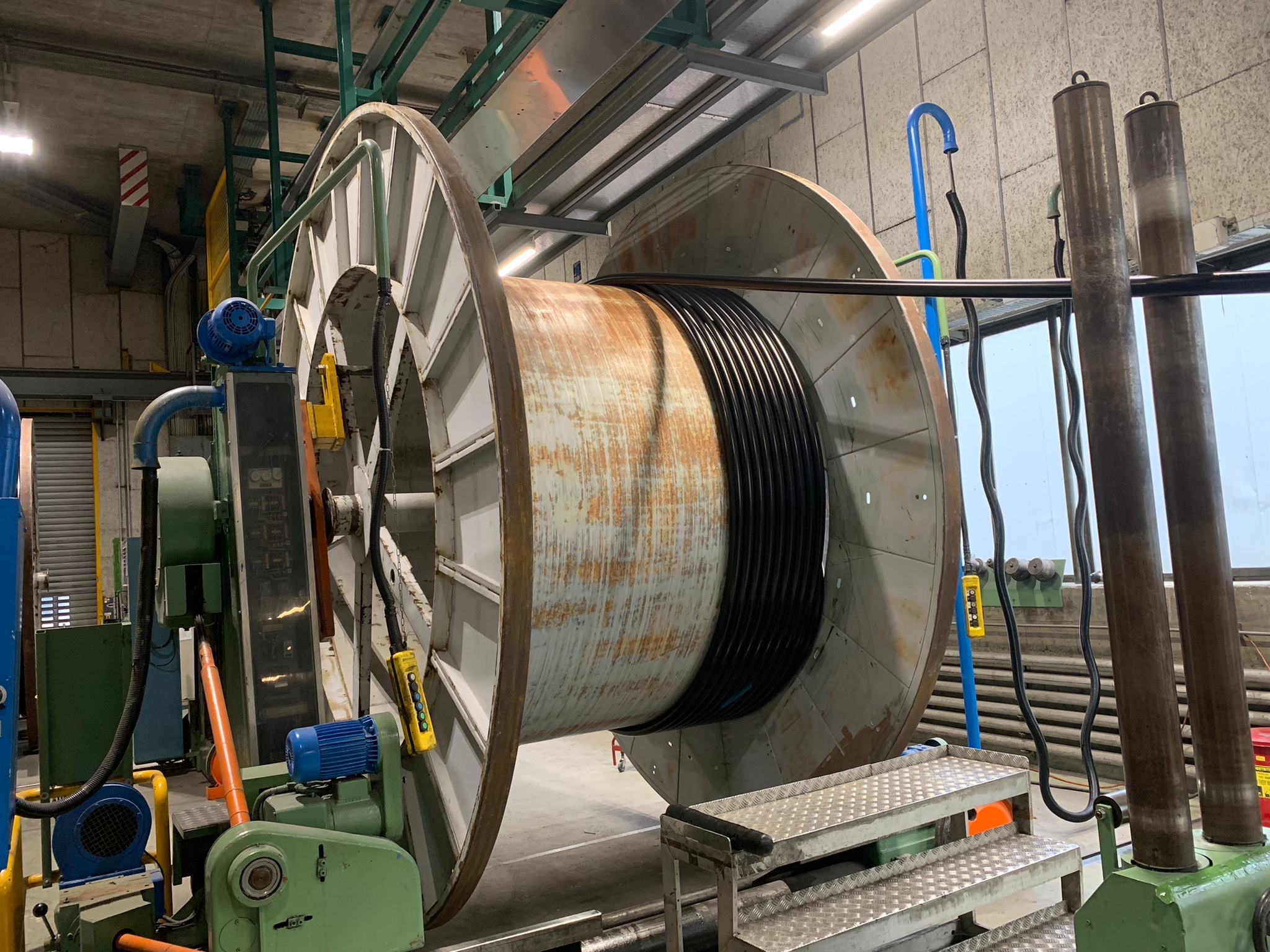
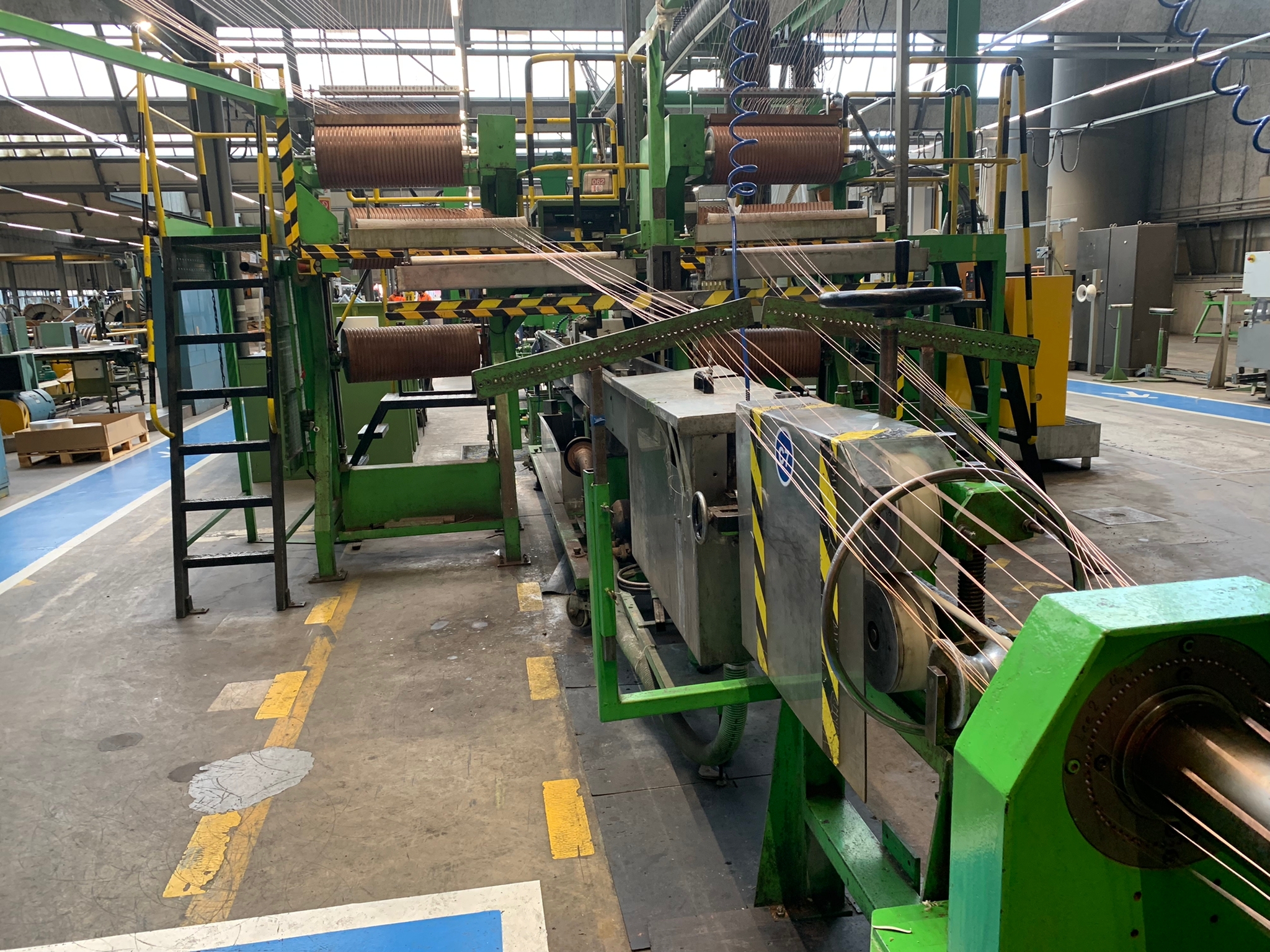
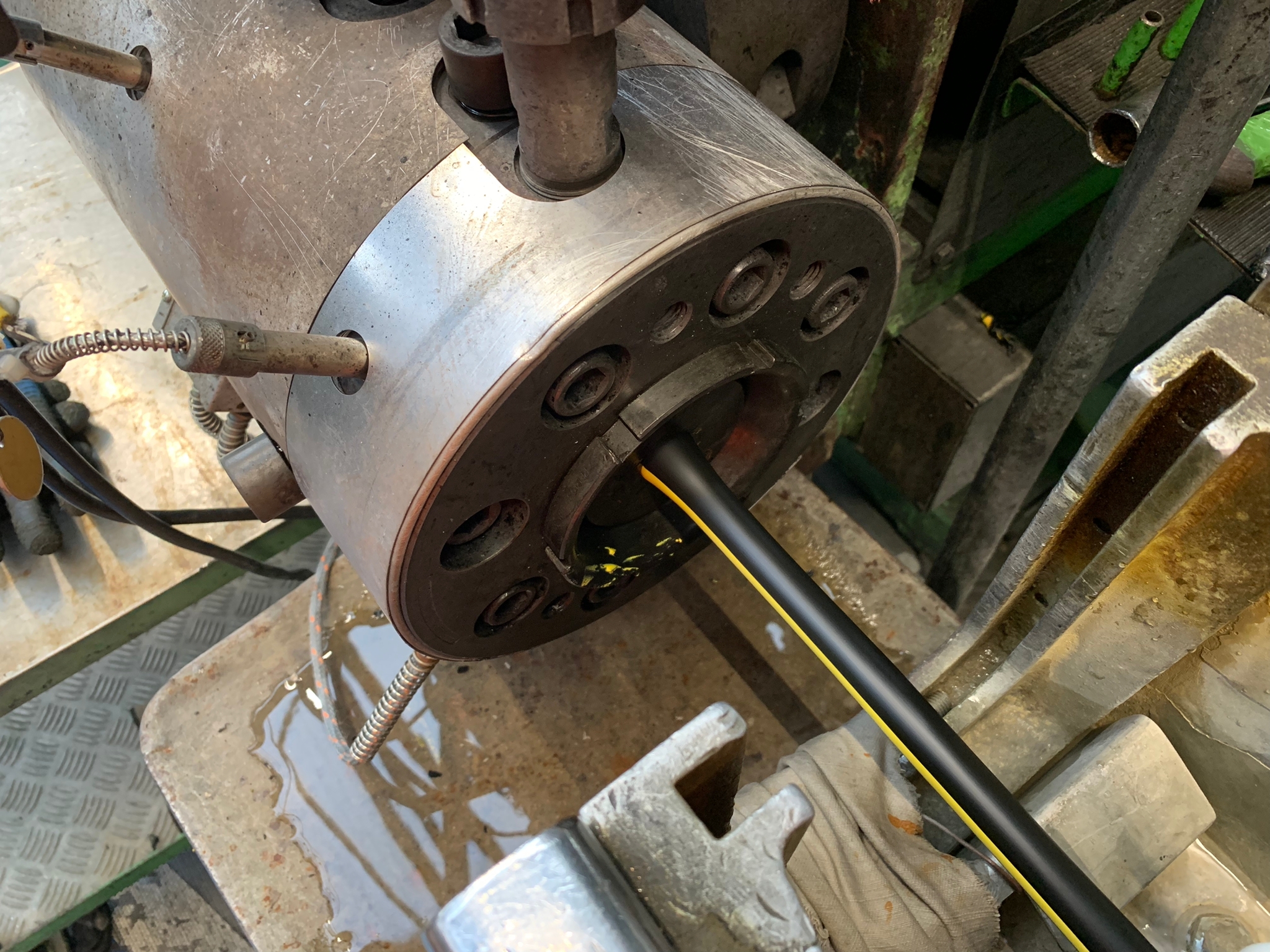
Our advantages
Personal support
By mail, by phone - whatever you prefer. We will be happy to advise you competently.
Short delivery times
We strive to process all orders quickly and thus enable short delivery times.
Large assortment
Choose from our wide range of products.